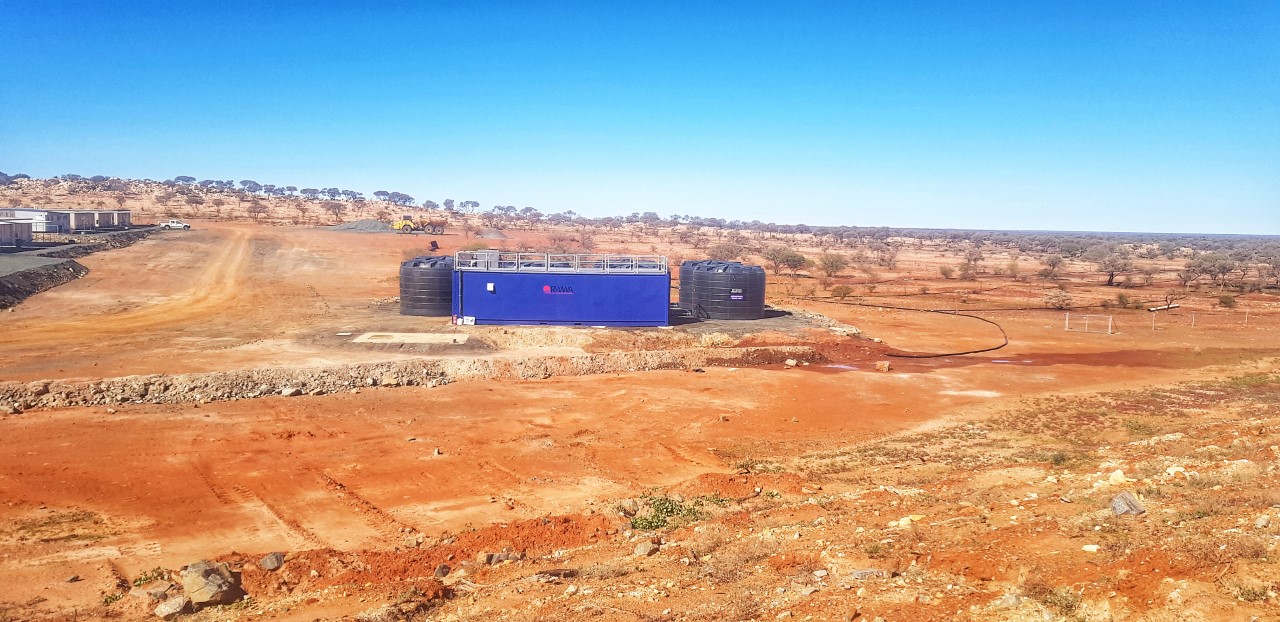
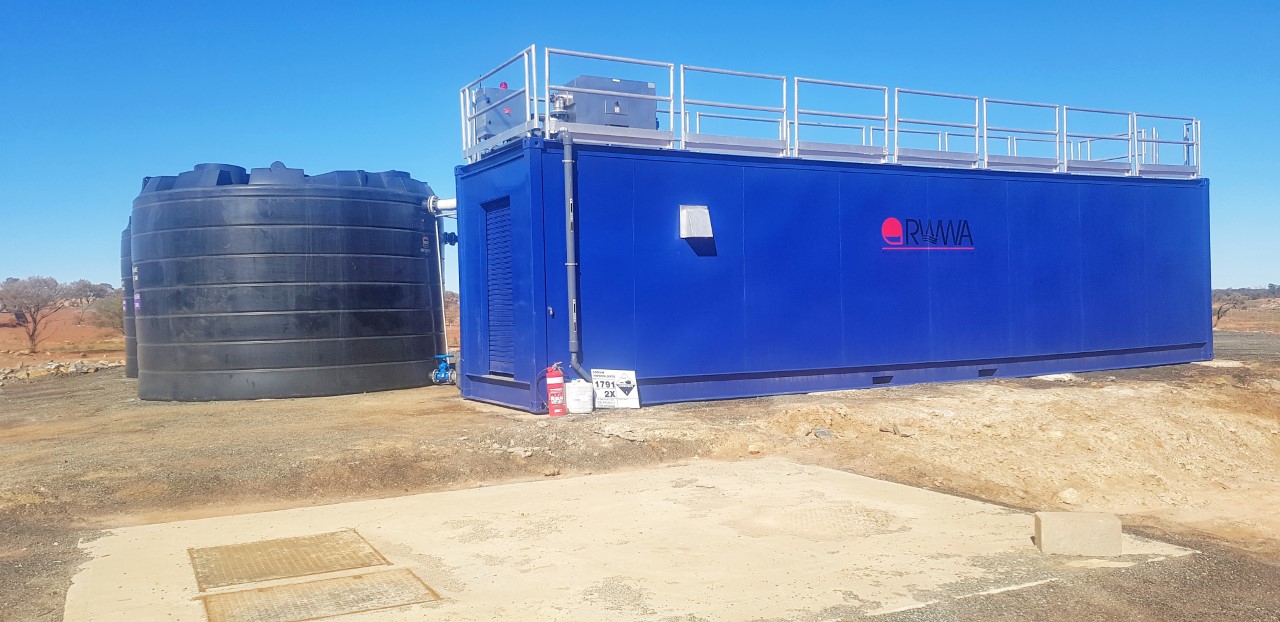
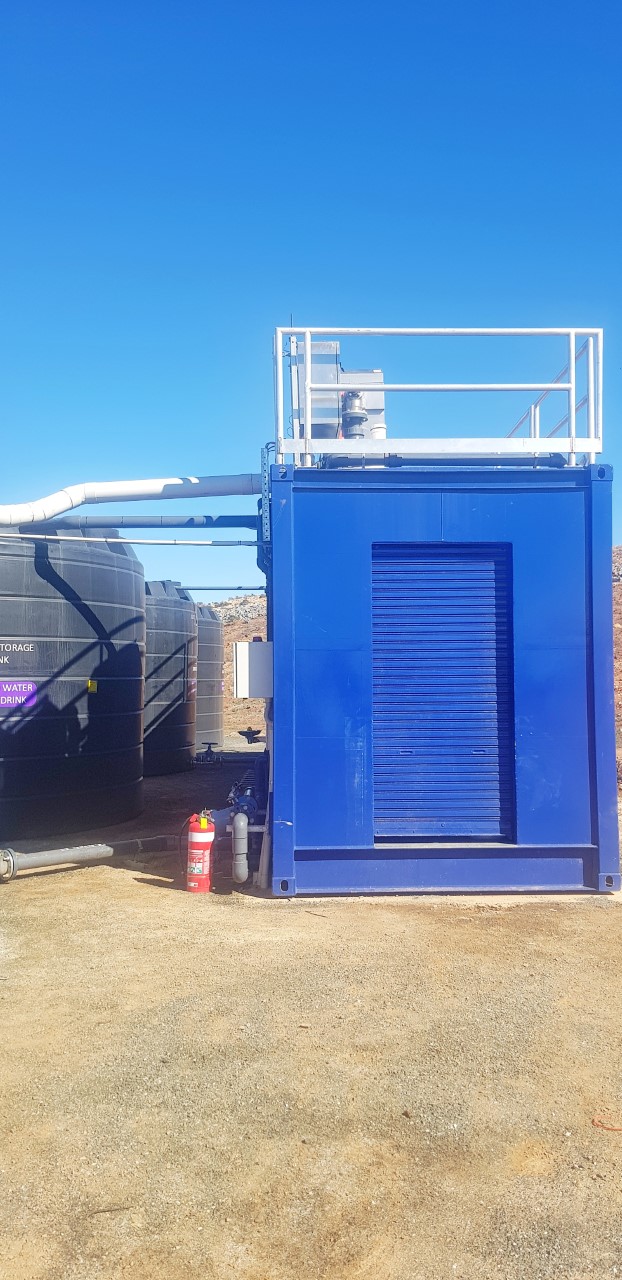
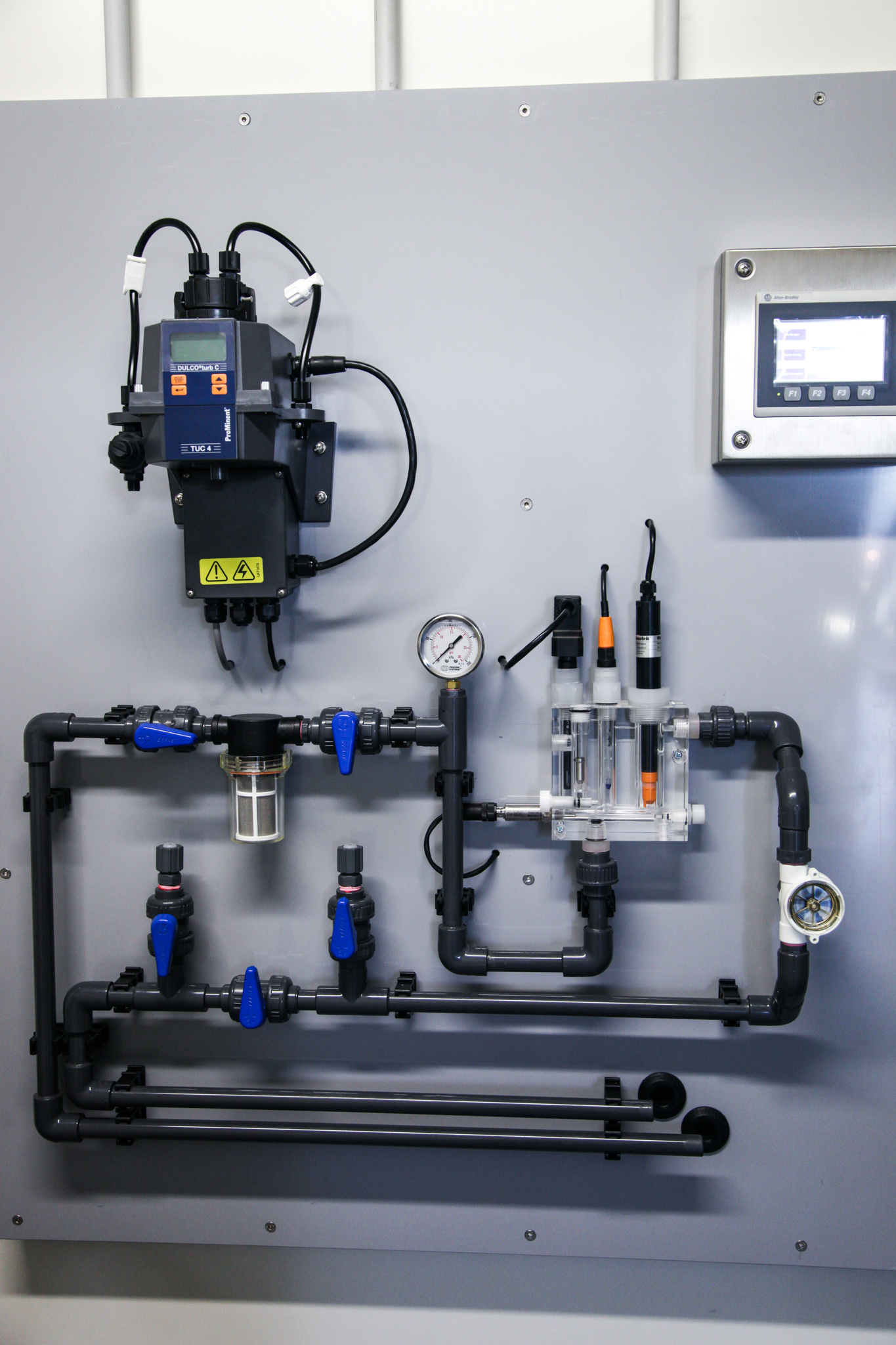
Client: Westgold Resources
Industry: Mining
Systems: EcoFarmer Wastewater Treatment Plant, Reverse Osmosis Water Treatment System
BACKGROUND
Westgold Resources, a top 10 Australian gold producer, recently began operations on their fourth Western Australian project – Cue Gold Operations. In order to manage the wastewater of their 200-man remote accommodation village at the Big Bell Underground Mine, Westgold approached RWTS to design and manufacture a wastewater treatment system. This same site also required a water treatment system to transform he local raw (bore) water into high quality drinking water as deemed by the Australian Drinking Water Guidelines.
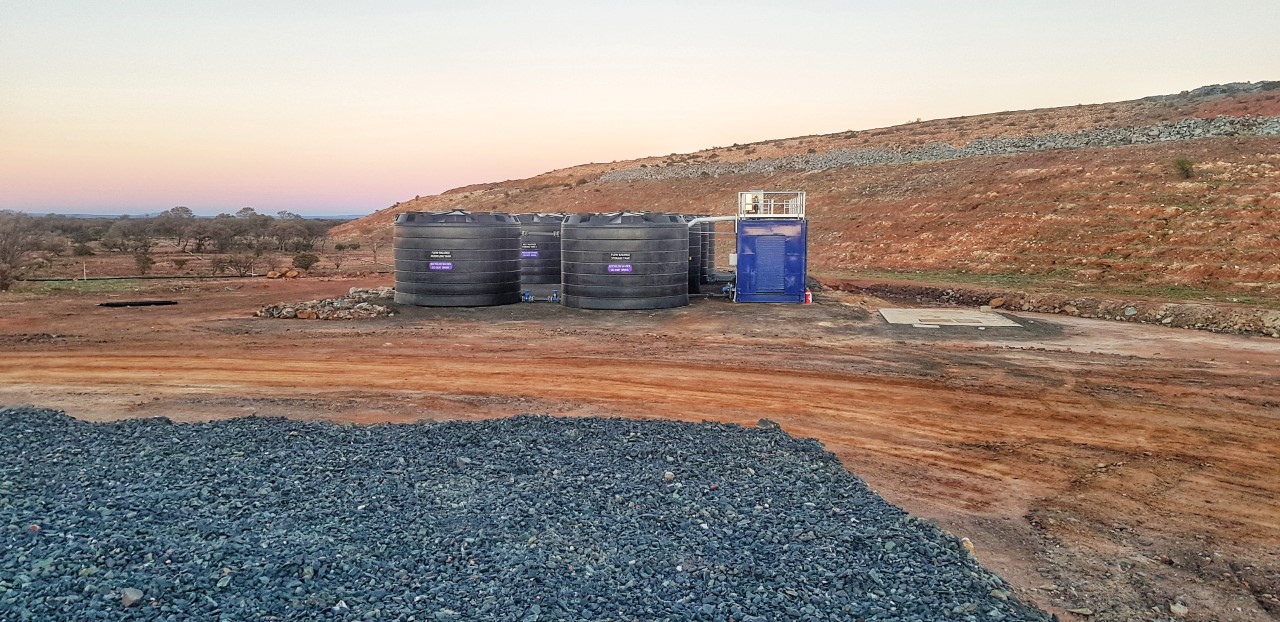
RWWA Solution
This project was an ideal candidate for the EcoFarmer 250 Wastewater Treatment Plant which utilises a Sequential Batch Reaction (SBR) process. Although this is a standard process throughout the water treatment industry, RWWA emphasised the functionality of the plant from the initial design stages. Through the seamless collaboration between our in-house engineering and electrical divisions, smart automation was integrated for enhanced productivity with less operator intervention.
How does the automation work?
The plant continually revises code as it observes the plant’s flow. When limited flow is achieved throughout the day, a standby code automatically seizes control of the plant and in peak periods the extended code will drive the plant.
In addition, Westgold Resources will reap the benefits of the EcoFarmer, that come as standard in this turnkey range, including:
– Robust steel construction to withstand harsh, remote environmental conditions
– Seamless transportability, attributed to the ISO shipping container design
– Premium Allen Bradley HMI (interface) and PLC control system
– Biological treatment process pre-approved by state regulatory bodies
Guaranteed & Certified Design
The design was accepted with process and structural certification by REPQ.
All stringent Western Australian department of health requirements where achieved, including a 20-year design life on the plant.
The structural steel shell was manufactured sandblasted, primed and painted with an International shipping coating internally. As part of our manufacturing process, spark testing was completed across the vessel to proactively identifying any potential issues with weld and coating. This ensured the integrity of the internal and external coating surface.
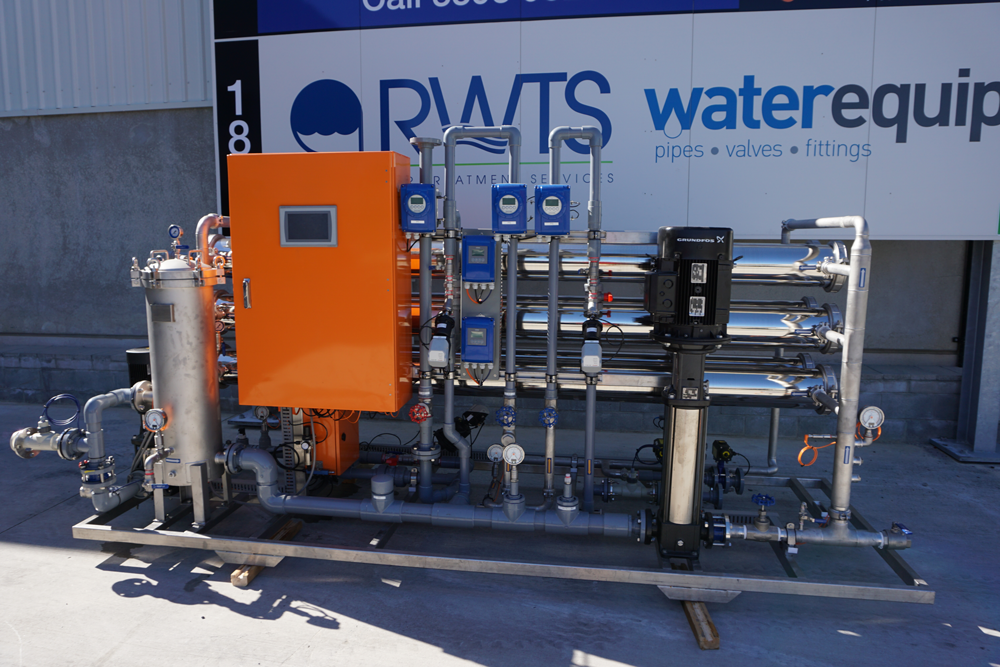
RWWA designed and manufactured a reverse osmosis potable water treatment system to meet the potable water requirements of the Westgold Big Bell remote workers’ village.
Built to Last
As the industry specialist in packaged water treatment systems, we decided to containerise the RO system. This allowed for ease of transportation and protection of the system from harsh rural environmental conditions.
For optimal insulation, the internal plant room was lined with 75 mm foam-filled panelling on the walls and ceiling, and air-conditioning system was integrated to ensure ideal operating temperature through the hotter and cooler months.
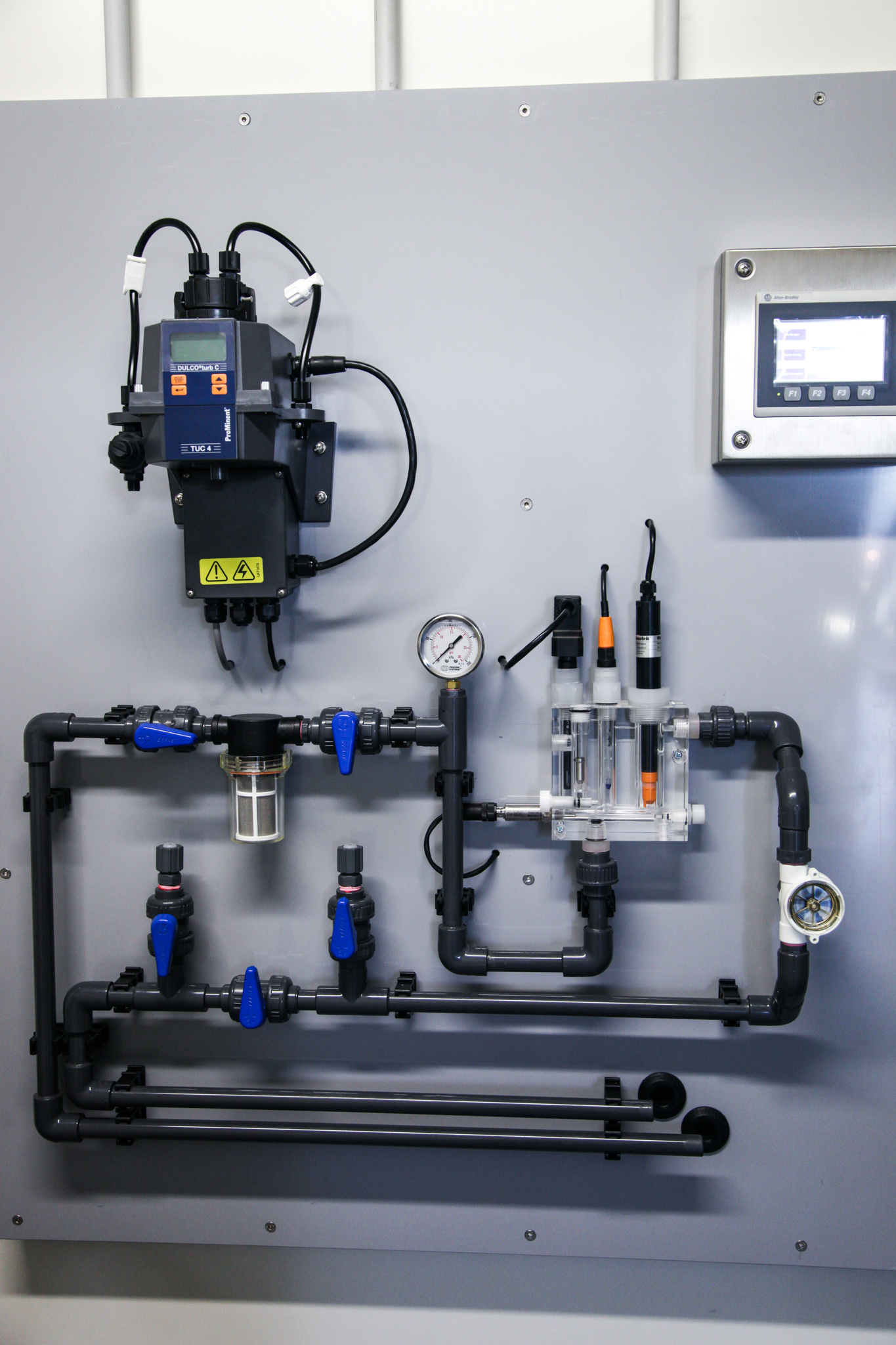
User-Centred Design and Automation for Streamlined Operation
The treated water recirculation monitoring and dosing control platform was our internal proprietary offering. This specialist feature is able to measure chlorine pH and conductivity, utilising the new range of Burkert flow fit cubes with gateway Ethernet, and display these levels in real-time on the PLC HMI plant platform.
Our internal programming and instrumentation division designed and custom-built the HMI to be single interface of all plant monitoring, streamlining plant observation and operation. This thoughtful feature allows Westgold to reduce operating costs and rapidly identify and respond to any potential issues.
As with all RWTS chemical injection systems, this Westgold system was fitted with Burkert Viton solenoids and Mazzi Venturi systems. Again, these offer fully programmable control through the HMI system, enabling the operator to take control at any time. A
The RWWA Brackish water reverse osmosis design also features flux targeting through flow metering with secondary pressure monitoring. This allows the RO system to maintain flux across the filter elements in permeate and concentrate streams through modulating v-notch ball valves. This is common on large scale membrane projects, however, in the price-driven remote camp market, it is often overlooked, and flows are set with manual tuning valves. This unfortunately is detrimental to the life of the membrane, resulting in more frequent membrane replacements and increasing the long-term operating costs of the plant.
Smart Technology for Flexible Monitoring & Control
RWWA uses the latest Allen Bradley HMI and PLC platform for full control of all our plants. These systems have a wireless router allowing for full remote dial-in access through site wifi. This is a must in the ever-changing water and wastewater servicing industry. It allows the plant performance and parameters to be viewed anywhere, anytime. Imagine the ease of troubleshooting over the phone with your site-based operator as you monitor the plant’s performance in real-time. That’s the RWWA difference.
Recent Comments